Robotic Depowdering for Additive Manufacturing via Pose Tracking
With the rapid development of powder-based additive manufacturing, depowdering, a process of removing unfused powder that covers printed parts, has become a major bottleneck to further improve its productiveness. Traditional manual depowdering is extremely time-consuming and costly, and some prior automated systems lack adaptability to different parts. We introduce a robotic system to fully automate depowdering. The key component is a visual perception system, which consists of a pose tracking module that tracks the 6D pose of powder-occluded parts in real-time, and a progress estimation module that estimates the completion percentage. Our depowdering system can remove powder efficiently for various types of parts without causing any damage. To the best of our knowledge, this is one of the first vision-based, fully automated depowdering systems for additive manufacturing.
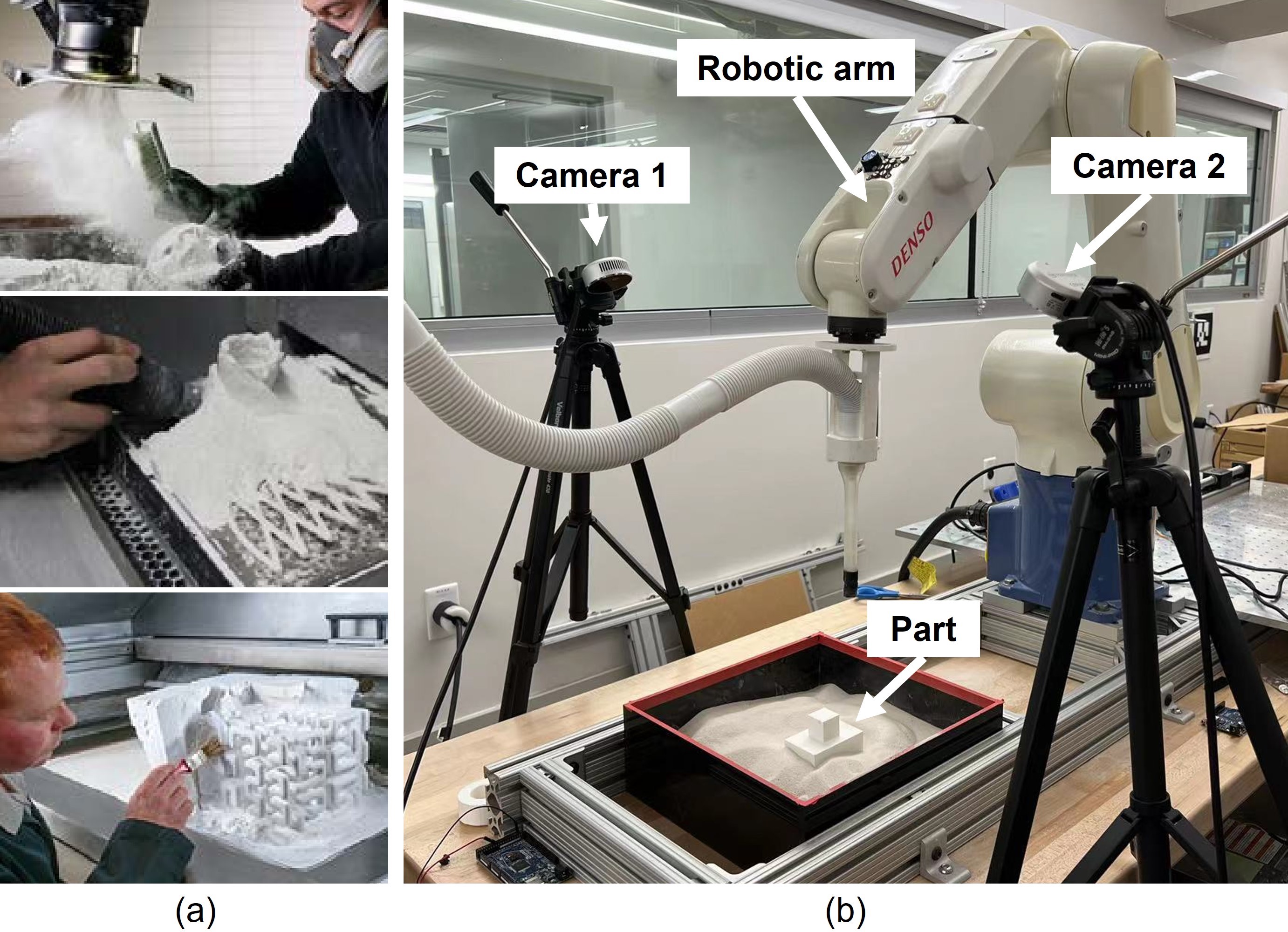
Robotic Depowdering System
The architecture of the depowdering system consists of a visual perception system (VPS), and a motion planning system (MPS). The VPS tracks the part pose in real-time, extracts the powder contour around printed parts, and estimates the depowdering progress. The progress is defined as the height ratio between the visible portion of the part and the complete part. Then, based on the estimated pose and the powder contour, the MPS generates a depowdering path along the outer contour of the visible part surface.
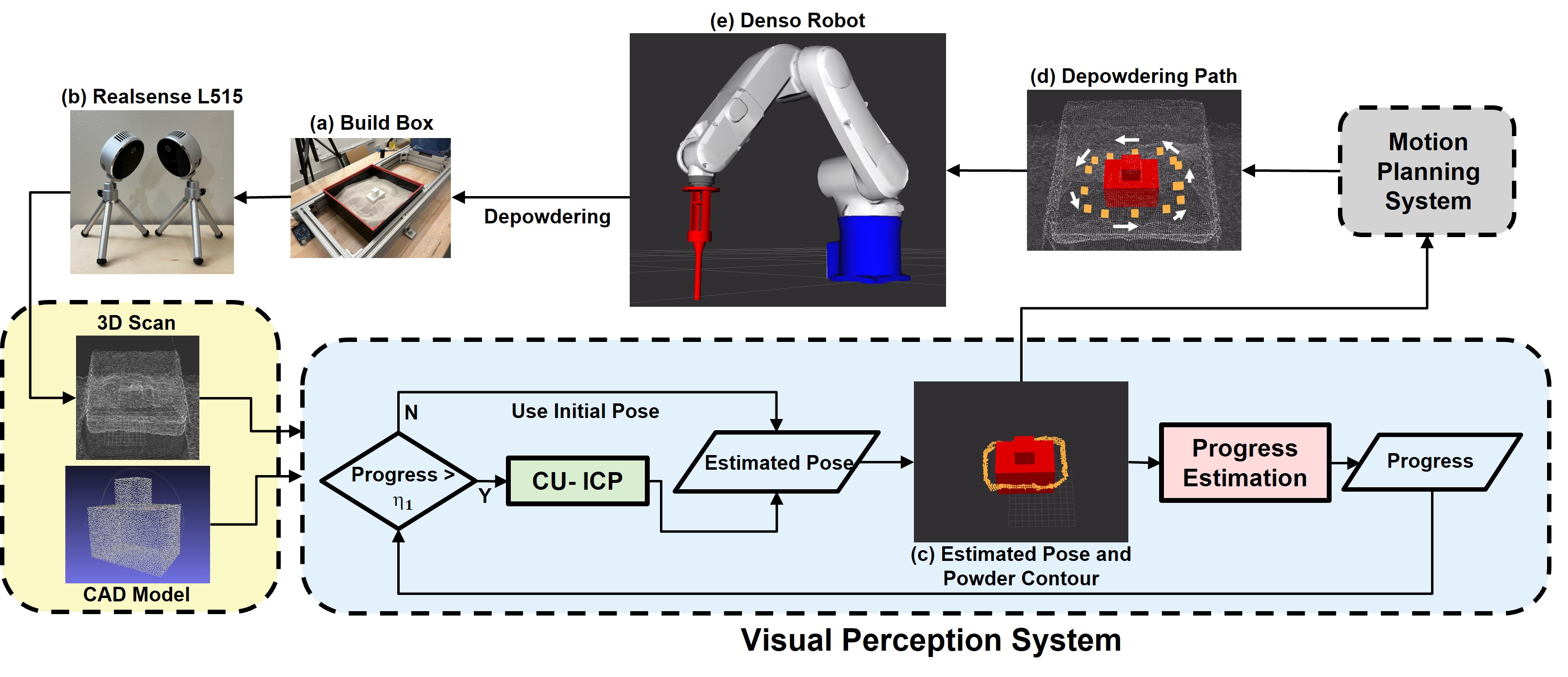
Visual Perception System
The goals of the VPS are to: (1) track the current 6D part pose in real-time. (2) identify the powder contour around the part and estimate the depowdering progress. With the known initial pose and the CAD model, we formulate the pose tracking problem as a real-time registration problem. The traditional ICP is able to align a source point cloud to a target point cloud by minimizing the L2 error without relying on feature extraction.
One major challenge for ICP is the target appearance variation. A common practice to address this is to update the template based on the current object appearance. However, neither using the entire CAD model as a template or update the template every frame by taking the overlap between the CAD model and the current point cloud scan is ideal. Because it either results in a mismatch between the template or the target or template quickly becomes erroneous
We propose a conditional template update strategy for ICP to avoid accumulated template update errors. Specifically, the template is updated only when the part appearance has changed significantly. In depowdering, this happens either when (1) more part surface becomes visible as more powder is cleaned or (2) printed parts have moved either by the depowdering tool or due to the loss of balance. Either scenario causes the powder distribution to change.
Video
Related Paper
BibTeX:
@article{liu2022robotic,
title={Robotic Depowdering for Additive Manufacturing Via Pose Tracking},
author={Liu, Zhenwei and Geng, Junyi and Dai, Xikai and Swierzewski, Tomasz and Shimada, Kenji},
journal={IEEE Robotics and Automation Letters},
volume={7},
number={4},
pages={10770--10777},
year={2022},
publisher={IEEE}
}